D CEO Healthcare
The Business of Healthcare in North Texas
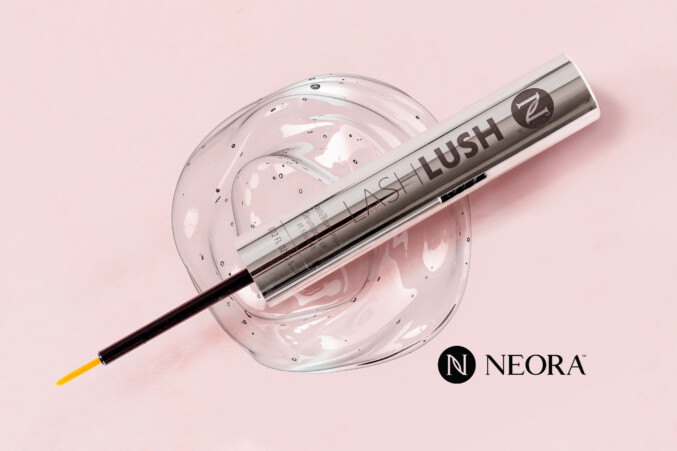
Business
Wellness Brand Neora’s Victory May Not Be Good News for Other Multilevel Marketers. Here’s Why
The ruling was the first victory for the multilevel marketing industry against the FTC since the 1970s, but may spell trouble for other direct sales companies.
By Will Maddox
Advertisement
Trending
Advertisement
Latest
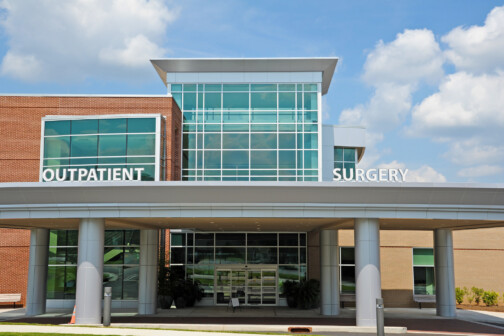
Commercial Real Estate
What’s Behind DFW’s Outpatient Building Squeeze?
High costs and high demand have tenants looking in increasingly creative places.
By Will Maddox
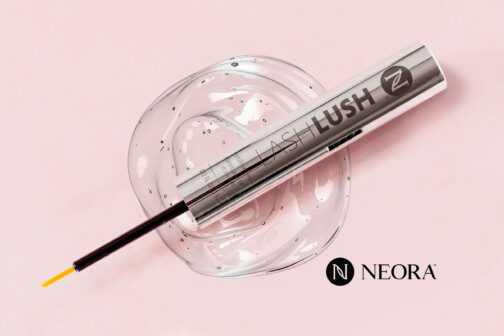
Business
Wellness Brand Neora’s Victory May Not Be Good News for Other Multilevel Marketers. Here’s Why
The ruling was the first victory for the multilevel marketing industry against the FTC since the 1970s, but may spell trouble for other direct sales companies.
By Will Maddox

News
Methodist Charlton Names New CEO and Steward Offloads Five More Hospitals for $1.1 Billion
Plus Texas Health Mansfield's new president and CEO, TimelyCare recognized by EY, and more.
By Bridget Reis
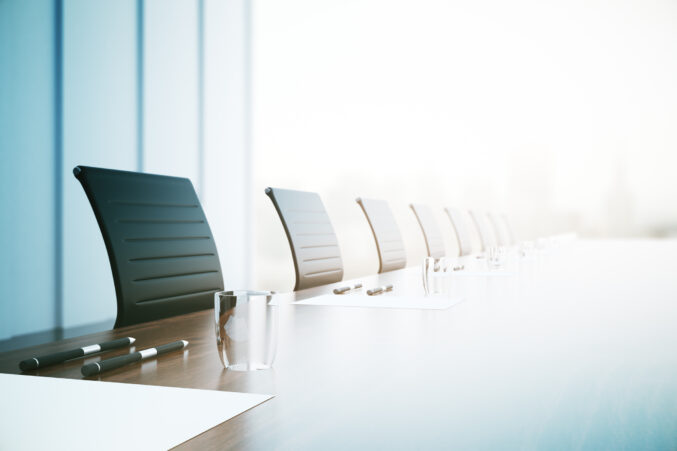
Healthcare
North Texas Healthcare Compensation: Who’s On Top?
Executives at Tenet Healthcare, McKesson Corp., and CHRISTUS Health lead the way.
By Will Maddox

News
Medical City Dallas’ New CEO and Hospitals Recognized for Price Transparency
Plus Texas Urology Specialists expands in North Texas and Business Group on Health honors Texas Health.
By Bridget Reis
Advertisement
Latest
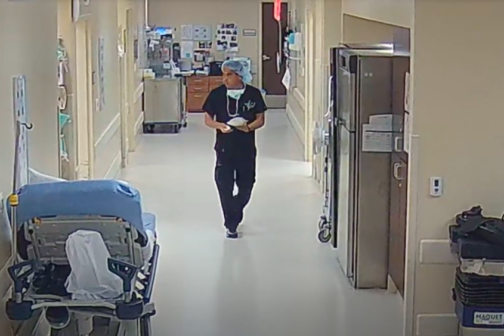
Healthcare
Convicted Dallas Anesthesiologist Could Face 190 Years for ‘Toxic Cocktails’ in IV Bags
Dr. Raynaldo Ortiz worked at the Baylor Scott & White Health facility after spending time in jail for shooting a dog and previous Texas Medical Board discipline.
By Will Maddox
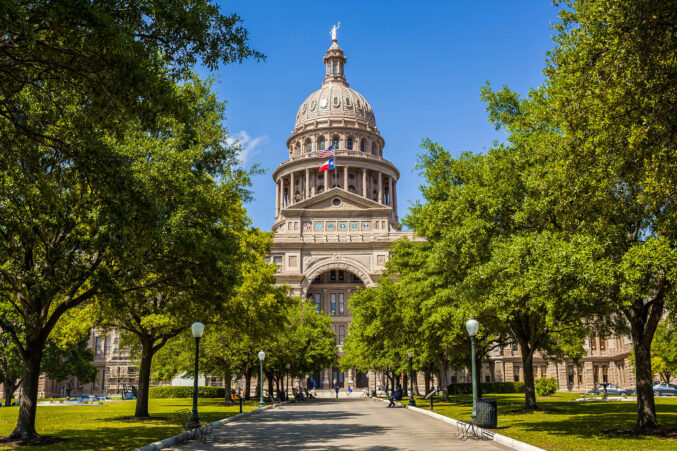
Policy
As Mississippi Nears Medicaid Expansion, Could Texas Be Next?
An Episcopal Health Foundation study found that Texas loses $7 billion in healthcare and lost productivity costs each year due to health disparities.
By Will Maddox
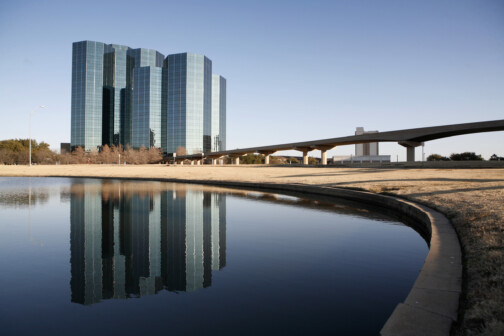
News
DFWHC’s Steve Love Named Chair-Elect of Irving Chamber and Medical City Again Wins ‘Best Place to Have a Baby’
Plus Red River Hospital's New CEO and Texas Recognized by Fortune as Best Place to Work.
By Bridget Reis
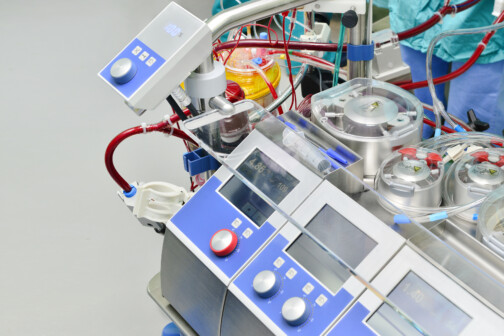
Healthcare
The Local Hospital Using Heat to Treat Cancer
First Baptist Medical Center is one of the only places in the country offering the innovative treatment.
By Will Maddox
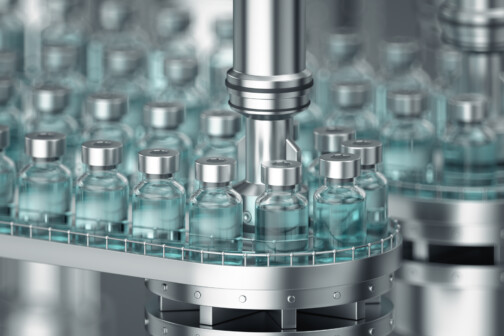
Healthcare
How Lantern Pharma’s AI Is Changing the Game
The precision oncology medicine company guided three drugs in the trial pipeline with uncommon efficiency.
By Will Maddox